轴承视觉检测技术,轴承被称为工业的“心脏”,是一种广泛应用的精密基础部件。
除基本型外,还有各种变型结构,如带防尘盖的、带橡胶密封圈的、带止动槽的等。基本型深沟球轴承主要由外圈、内圈、钢球、保持架、铆钉组成。
目前我国轴承产业规模已居世界轴承总量第三位,然而,在成品轴承外观检测上,基本依赖于人工,在工业领域,质检要想摆脱人力就必须进行技术升级和转型。
保证出厂轴承的良品率至关重要
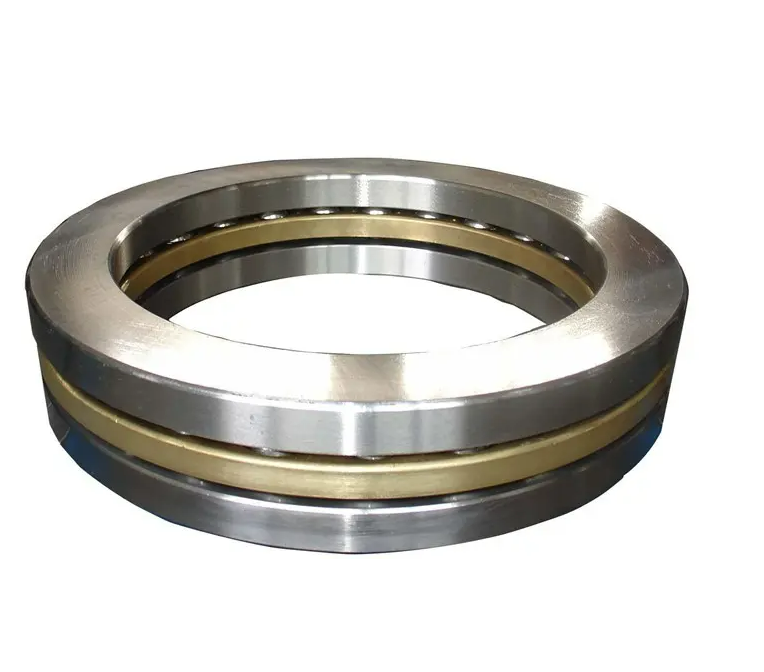
轴承作为现代机械设备中的重要零部件,主要功能是支撑机械旋转体,降低运动过程中的摩擦系数,并保证其回转精度。
在生产中,质检是重要的一环。通常情况下,质检员采用人工肉眼观察、手指转动轴承等质检方式挑出表面有油污、划痕等缺陷的轴承。
但质检结果易受人为因素影响,检验标准难以保持一致,稳定性差且易漏检,始终不能做到良品率100%。
就汽车而言,汽车的动力、可靠性、安全性和舒适性都与其息息相关。
因此,保证出厂轴承的良品率至关重要。
轴承常见的表面缺陷一般有以下几种:
1.麻点
零件表面呈分散或群集状的细小坑点,呈黑色针孔状凹坑,有一定深度,个别存在或密集分布。形成原因为金属表面疲劳,在滚动接触应力的循环作用下,金属亚表面形成微观裂纹,并逐渐发展成凹坑状。
2.擦伤
零件表面因滑动摩擦而产生的金属迁移现象,其形态特征为沿轴承零件的滑动方向,并具有一定的长度和深度的表面机械性损伤,这种缺陷多发生在轴承零件的工作面。
3.裂损
轴承零件金属的连续性遭到破坏而产生的损伤,呈现线状,方向不定有一定的长度和深度,有时肉眼不可见,磁化后有聚粉现象。
由于轴承表面缺陷形态各异,有些缺陷形态差别很大,很难找出这类缺陷的共同特点,造成识别上的困难。
有些缺陷目标的空间分布范围由单一连通的空间区域组成,而有些缺陷目标则可能由多个子区域组成;有些缺陷目标具有相当大的形状任意性和复杂性,并且不同类别的缺陷形状有可能相当接近,从而使目标和特征之间失去一一对应关系。有些非缺陷,如油印与缺陷非常相似,可能被误认成缺陷。
基于机器视觉技术轴承缺陷检测应用
众所周知,3C电子制造行业要求使用无尘车间生产,为AI质检提供了良好的环境。然而,轴承零部件行业的生产环境却要差很多,即使是号称使用“无尘车间”的成品轴承生产,其环境也只是相对干净和无尘,却无法与3C电子行业的无尘车间相提并论。
其次,轴承外观检测往往依赖于人,对工艺、要求的认知极大程度上依赖于行业经验的判断,轴承缺陷种类繁多,如端面缺陷、外径缺陷、内径磨削烧伤等,有些瑕疵普通人甚至很难用肉眼观测得到。
这种情况下,对传统的检测方式无疑提出了很大的挑战。
近几年,机器视觉在轴承行业的发展突飞猛进,已经实现的功能主要如下:
宏观缺陷的检测
1)滚动体的数量和位置识别与判定。
2)密封件的标识内容、形状、外观的识别与判定。
3)套圈表面、滚子表面宏观裂纹、磕碰等缺陷的识别与判定。
微观缺陷的检测
1)轴承零件半成品的尺寸形状检测与判定(精度±0.01mm)。可实现锻件、车件、保持架、密封圈等主要尺寸精度在0.01mm以上的检测。目前已经稳定实现,并有不少实际应用。
2)轴承零件成品的尺寸形状检测与判定(精度±0.001mm)。由于成品零件尺寸形状精度普遍达到0.001mm,通过单纯的光学成像原理来检测很难达到其精度等级。目前国内有一些科创企业通过后处理算法的优化,对检测精度进行了大幅的提高。
3)轴承零件表面微观裂纹、麻点、磕碰伤等缺陷的识别与判定。
机器视觉智能在线检测,摒弃繁琐低质的人工肉眼检测方式,提升并改进轴承品质。
|